I started with the line across the back of the engine compartment. It was not too difficult considering the number of bends in the piece. I kept the original so I could better duplicate the appearance and location of each bend. In the pictures the lines are just mounting with some old original bolts I've not bothered to clean up yet. The line looks crooked in the picture but it is not.
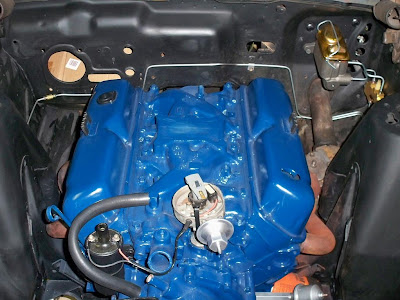
Since I'm adding disc brakes to the front but using rear drums, I next plumbed in a residual pressure valve. If not for needing this piece, I could have reconnected the original rear line to the proportioning valve. However, I took the opportunity to replace the portion of the line which leads from the proportioning valve to under the driver footwell. I installed the residual pressure valve at this point and then continued with the original line (to be replaced later).
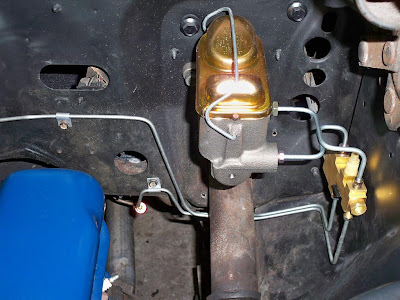
The last step was mounting the rubber caplier hoses so I could bend up lines for each of the front brakes. I completed the passenger side with no trouble. The driver side I wasted three lines of tube creating. Once I had all the bends correct, I then messed up flaring the line. I'll finish this side in the morning. Hopefully, I'll have better luck with it then.
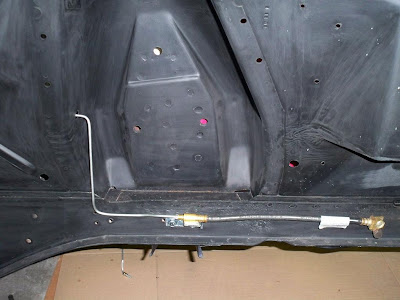