In order to remove the steering box, I first needed to take out the driver side exhaust manifold and z bar. The exhaust manifold on my car are very unique. It appears someone took a shorty style headerm, cut it where the primary tubes meet, and then just welded the exhaust solid from that point to the tailpipe. As a result, I needed to cut the exhaust near the bellhousing so I could remove the manifold.
It took a little while to find a way to remove the exhaust. It was obviously not made for the car so it was a very tight fit. However, I did get the exhaust removed. It has 1 5/8" primary tubes which are of unequal length. The exhaust on the car is 2 1/4" outer diameter. The only identifying mark on the exhaust is the number 603 09 02 on the exhaust flange.
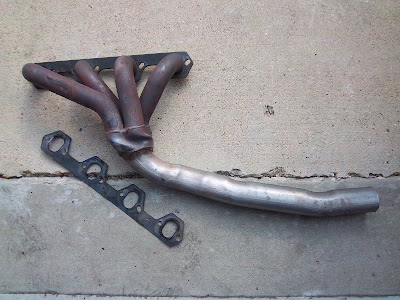
Once the exhaust was out of the way, I removed the steering box. I was able to pull it out through the area right beside the head. I did not need to remove the export brace or anything. The job was no doubt made easier by the fact there was no floorboard in the way so the long shaft could move around inside the car without any interferance.
I sent Stanger an email and then packed the steering box up for shipment. I'll wait until I hear back from him before shipping it off. I'd like to make sure he has time to do the rebuild before spending the money to ship it to him in San Antonio.
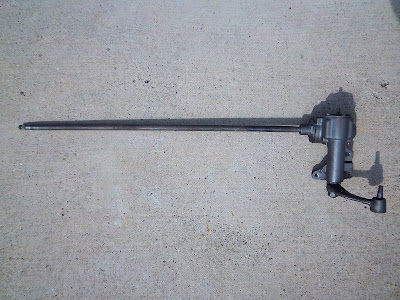
01/03/11 - I received an email back from Randy (Stanger) this morning stating he is still rebuilding steering boxes. He said he would be able to get to mine in early February. I shipped it to him for $21 at UPS.